We care about sustainability, both in our education program and ship construction.
All construction methods, materials, and equipment for Matthew Turner were selected with attention to their suitability for design functions, aesthetics, and the environmental impact. Other factors included analyzing the method by which these materials were obtained (i.e., equipment uses, carbon footprint, etc.) and what happens at the end of the use cycle.
Project Director Alan Olson and former Construction Superintendent Marc Bauer size up a log for the keel of the ship. Bruce Berry looks on in the yard at Berry’s Mill. Berry’s Mill in Cazadero, CA is the local FSC-trained sawmill cut all of the Doug Fir donated by the Conservation Fund.
Wood from Sustainably-Managed Forests
Wood is the primary building material and also the most eco-effective. Wood can be salvaged and reused many times, ultimately decaying and returning to the earth as a biological nutrient.
Our Ship is built from local Forest Stewardship Council Certified lumber. The best forests for providing this range of goods and services are those with a diverse natural structure of native species, different-aged trees, standing snags, down wood, and complex ecological processes—in short, many of the characteristics we associate with older forests. Stewardship forestry employs management and harvest techniques that foster these qualities.
The other primary wood being used is Oregon White Oak from Sustainable Northwest Woods. This beautiful, rot-resistant wood is logged from small family-held forests where the health of the entire forest is maintained through very selective cutting. Everything SNW carries is from the Pacific Northwest and grown on forests managed either to the standards of the Forest Stewardship Council (FSC) or as part of Healthy Forests, Healthy Communities Partnership. Healthy Forests, Healthy Communities is a stewardship program developed by Sustainable Northwest that is working to restore native ecosystems. SNW is 100% committed to sustainable wood – it’s their entire product offering, not just a small percentage of what they carry.
The fir that was donated by the Conservation Fund is being milled at Berry’s Sawmill, a local, FSC trained, family-owned sawmill in Cazadero, CA. The Berry family moved to the area in the latter part of the nineteenth century and established the town of Cazadero. In 1941, Loren Berry founded the sawmill with funds from his father after working for some time in the logging industry.
After World War II Loren Berry made a commitment to forest preservation and sustainable harvesting in the Sonoma/Mendocino area. Rather than clear-cutting and burning to clear land for grazing the Berry’s supported sustainable harvesting and forest stewardship. As a result of their efforts there are now more trees growing in the area than there were in 1941
Our Partners in Sustainable Forestry
The principle wood we will use is locally grown and harvested Douglas Fir, which will form the major structure, masts and hull of the vessel. The Douglas Fir for our ship has been generously donated by the Conservation Fund from their 50,000 acres of sustainably managed forests in Mendocino California. The Conservation Fund is rehabilitating these forests to be commercially productive through stewardship management while also creating a healthy and biologically diverse forest. By employing a mix of conservation and preservation techniques the Conservation Fund is able to protect portions of their forests from logging. This preservation sequesters carbon in the forest and allows to the Conservation Fund to generate substantial income by selling carbon credits.
After wood, metals are the next largest component used in ship construction and can be classified as “technical nutrients” if they are properly recycled back into the production stream. As an example, forty tons of lead will be safely contained and sequestered when used as ballast and batteries aboard our ship. Lead with a low melting temperature can easily and indefinitely be returned into the product stream.
Copper-based alloys that will hold the ship together and will be used in electrical wiring and electrical components can simply be recycled as a “technical nutrient.” Smaller amounts of steel and stainless steel will also be returned for reuse. More challenging however, are the very small amounts of rare metals that are used in shipboard electronics and will require sophisticated recovery methods.
Coatings, paints and glues can be a source of pollution in their production, application and end-cycle due in part to the difficulty of isolating, retrieving and recycling these substances. Fortunately, today there are many better options available than ever before. For example, marine bottom paints were designed in the past to be as toxic as possible to organisms that grow on boat bottoms, without regard to the impact on the larger marine environment. Driven by consumer demand for “greener” products and tighter environmental regulations, new paints are now available that work just as well to keep bottoms clean and are considered eco-friendly.
Plastics represent a more difficult challenge. While many can be recycled, they are usually ‘down-cycled’ and soon become less valuable ending up in landfills or disposed of as fuel in incinerators with environmental consequences that are not fully understood. All of the electronics and computers contain hard-to-recycle plastics and exotic heavy metals and complex toxic compounds. Few manufactures consider the endgame of their products or take responsibility after they are sold. We will look for the best outcome for every piece of electronics that comes aboard our ship.
Dacron Sails and lines represent the largest plastic component used onboard our sailing ship. Modern sailors know the huge advantage in efficiency and longevity that Dacron offers. We are researching the fate of recycled Dacron generically referred to as PET. There is a non-mechanical recycling process being developed that breaks down the materials within the PET plastic to their base building blocks so that they can be recombined to create essentially virgin quality PET. This has the potential of making PET plastic infinitely recyclable without any loss of physical properties.
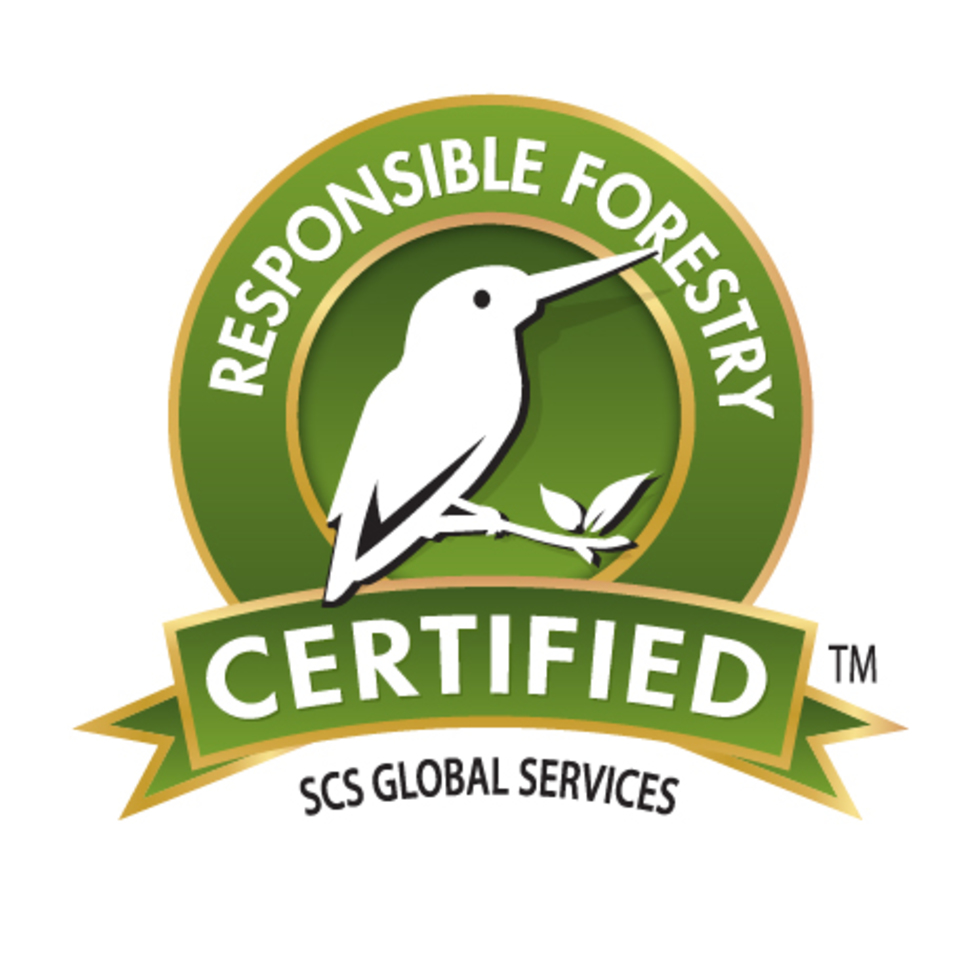
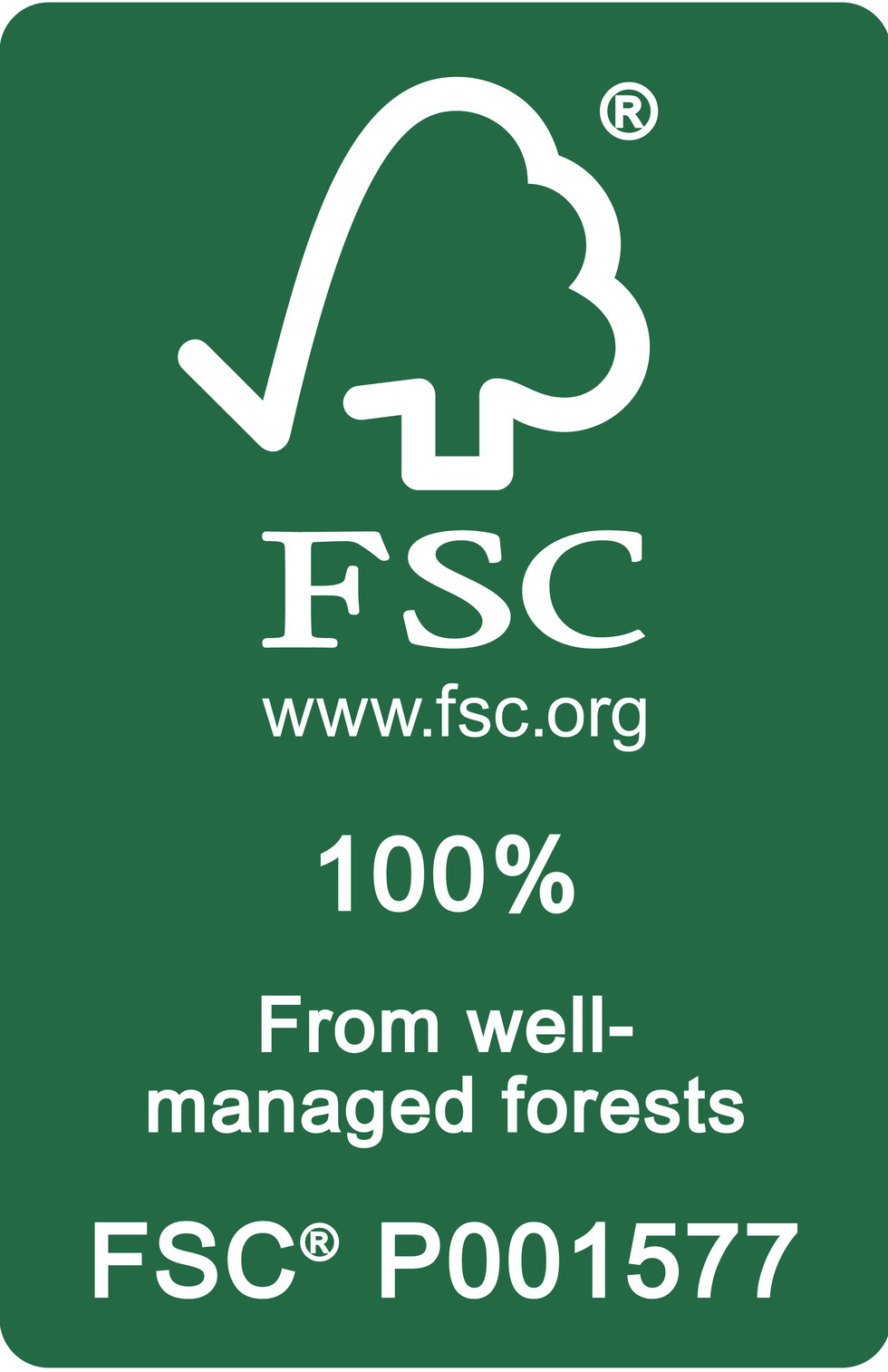
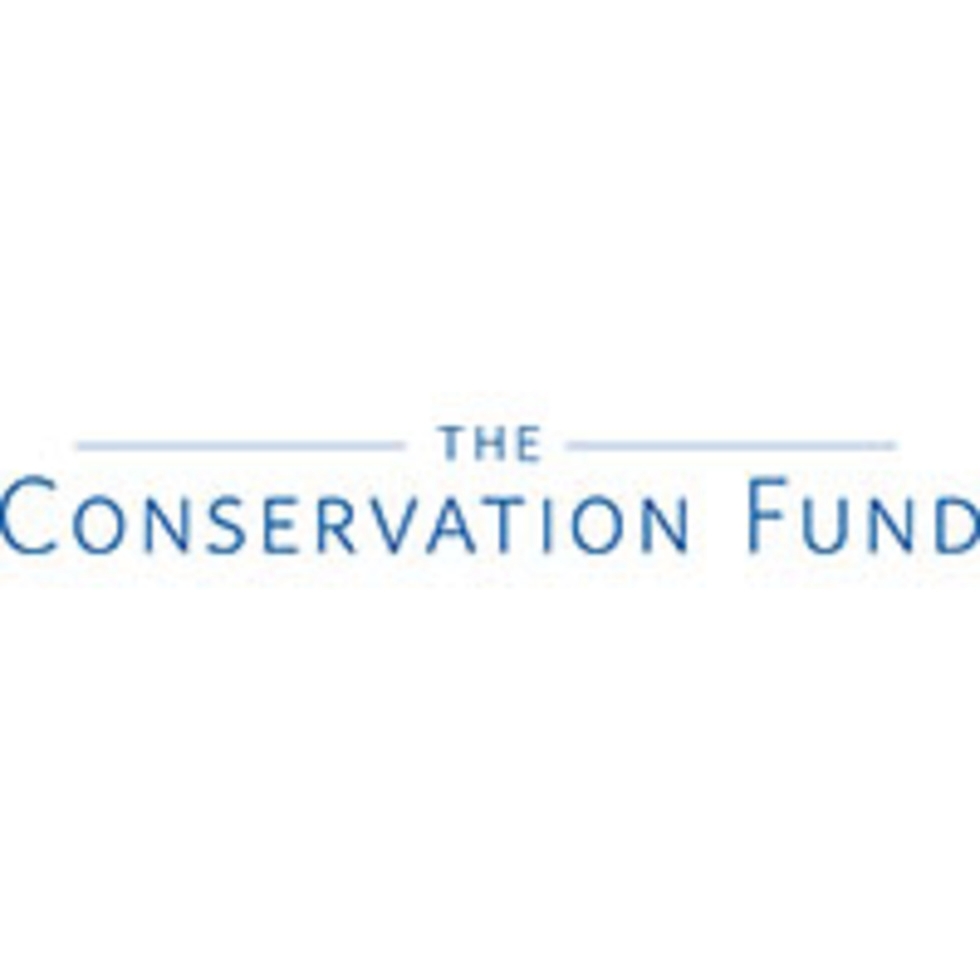
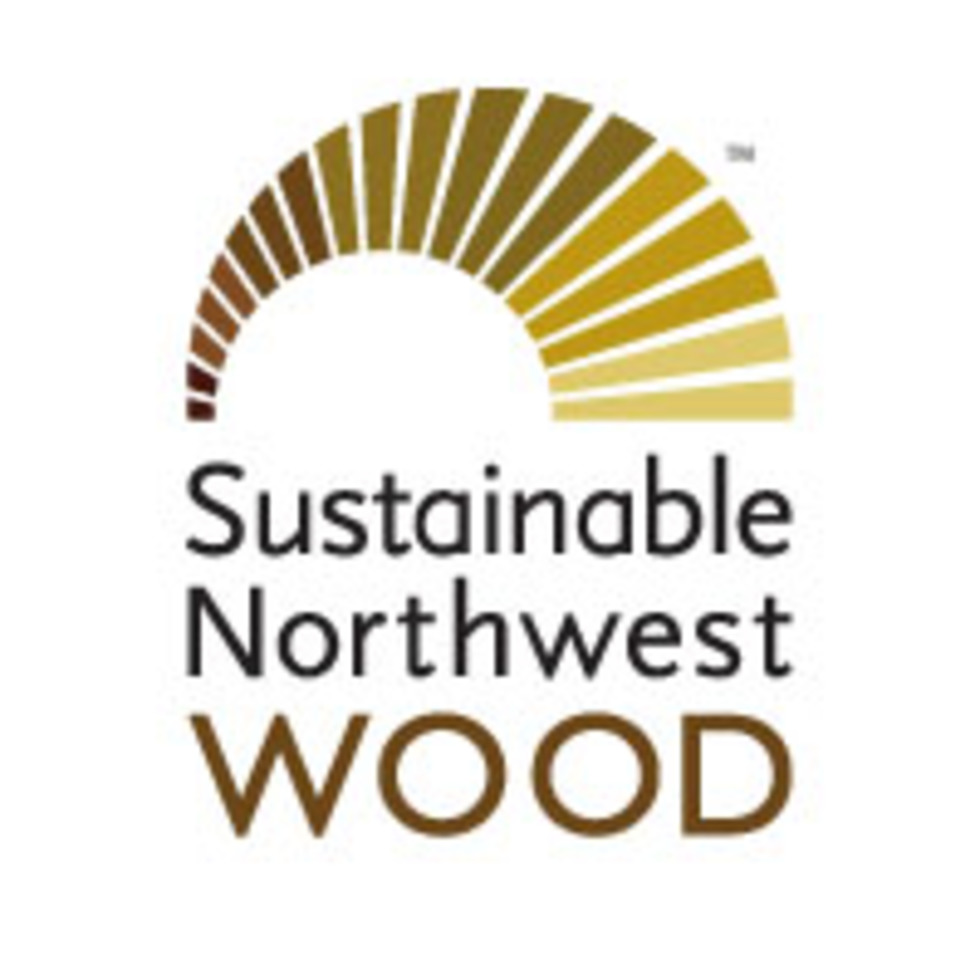